The emergence of e-commerce has revolutionized the business environment, raising customer expectations to new heights. Rapid order fulfillment has become a paramount requirement, presenting fresh obstacles for retailers operating in a highly competitive market.
Effective inventory management and a streamlined supply chain are indispensable for meeting these expectations. Retailers must ensure the prompt availability of accurate product quantities. Inadequate inventory management can result in unmet orders, lost shipments, and delayed deliveries.
To tackle these challenges, retailers must utilize pertinent metrics to ensure timely order fulfillment. One vital metric is lead time, which plays a crucial role in planning reorder activities and optimizing overall inventory management.
Lead Time and Its Impact on Business Operations
Lead time refers to the duration between the initiation and completion of a process. Companies analyze lead time in various areas such as manufacturing, supply chain management, and project management, during pre-processing, processing, and post-processing stages. By comparing lead time results against established benchmarks, they can identify areas of inefficiency.
Reducing lead time can enhance productivity, streamline operations, and increase revenue. Conversely, longer lead times can have adverse effects on sales and manufacturing processes.
Key Takeaways | |
---|---|
Definition | Lead time is the duration required to complete a process. |
Application | In manufacturing, lead time involves creating and delivering products to customers. |
Calculation | Lead time is calculated by adding procurement, manufacturing, and delivery times. |
Influencing Factors | Raw material shortages, transportation breakdowns, labor shortages, natural disasters, and human errors can impact lead time. |
Improvement Strategies | Companies can improve lead times by implementing automated stock replenishment and just-in-time (JIT) strategies in certain cases. |
Step-by-Step Guide to Calculating Lead Time in Your Business
When it comes to inventory forecasting, taking lead time into account is vital. The calculation method for lead time varies based on the specific context, as different processes have unique components that impact their overall duration.
In the realm of inventory management, lead time refers to the time elapsed between placing a purchase order to restock products and receiving the order in the warehouse. It’s crucial to acknowledge that lead times can differ depending on the suppliers involved in the supply chain. When multiple suppliers are involved, lead times tend to be longer, emphasizing the importance of thorough consideration and planning to accommodate these variations.
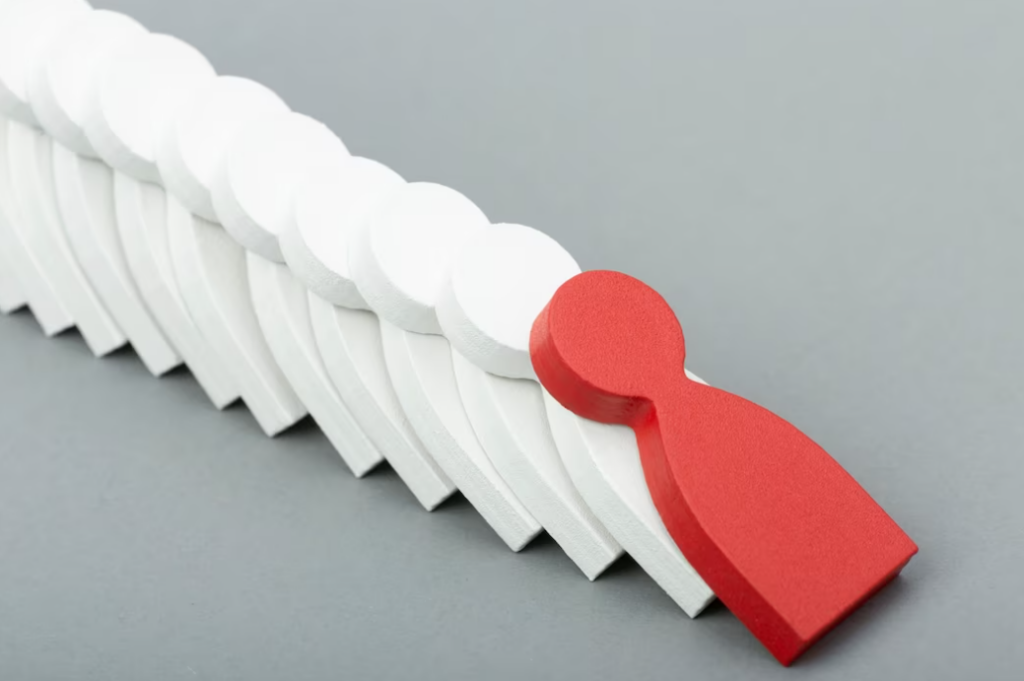
The Formula for Lead Time Calculation in Manufacturing and Inventory Management
To calculate lead time, you need to determine both the supply delay and the reordering delay. You can use a lead calculator to save time. Here are the steps to calculate it:
- Determine the reordering delay: This involves factoring in the time required for the supplier to accept and process the order. For instance, if the supplier only accepts reorders once a week, and you place an order four days before the day the supplier accepts the order, your inventory will need to last an additional four days. This additional four day is known as the reordering delay;
- Determine the supply delay: This is the time it takes for the shipment to reach your inventory;
- Sum the supply delay and the reordering delay to calculate lead time: The lead time formula is simply the sum of the supply delay and the reordering delay.
Therefore, the lead time formula is:
Lead time = supply delay + reordering delay
Lead time has a direct impact on your total inventory levels. Longer lead times require you to hold more stock in your inventory, making deliveries more unpredictable and forcing you to rely heavily on demand forecasts to make orders. Once you have calculated your lead time, you can take corrective measures to reduce it.
Illustrative Lead Time Calculations
To gain a clearer understanding, let’s examine some examples of lead time calculations in action. Consider a jewelry brand named Alex Munroe, a customer of Brightpearl, which offers both pre-made and made-to-order necklaces. To determine the lead time, the brand needs to consider pre-processing, processing, and post-processing stages in its calculations.
For made-to-order necklaces, let’s assume that orders are picked up the day after they are placed (pre-processing). The processing stage involves creating the item, which takes approximately two weeks. Once the necklace is ready, it is packaged and sent out (post-processing), taking three days for delivery to the customer.
Using the formula for calculating manufacturing lead time, we can add the durations of pre-processing, processing, and post-processing:
- 1 day (pre-processing) + 14 days (processing) + 3 days (post-processing) = 18 days
On the other hand, placing an order for a pre-made necklace may have a shorter lead time, requiring only two days in the processing stage:
- 1 day (pre-processing) + 2 days (processing) + 3 days (post-processing) = 6 days
Having accurate lead times for both pre-made and made-to-order products is crucial to enhance customer satisfaction and establishing clear expectations. By providing customers with reliable information regarding lead times, Alex Munroe can deliver a positive experience, ensuring customer satisfaction and fostering transparent communication.
Tips to Reduce Lead Times and Optimize Inventory Management
To effectively reduce lead times and optimize inventory management, you need to have a thorough understanding of your supply chain processes. Here are some factors to consider:
- Document your supply chain journey: Identify all the points along the way where you can expect waiting times. Plan for the worst-case scenarios as well as seasonality;
- Increase the frequency of orders and decrease the volume: Instead of ordering a large amount of inventory, order smaller amounts that take less time to manufacture and ship. Your inventory is then replenished more frequently and more consistently;
- Incentivize your suppliers: Work a lead time clause into your contracts with suppliers. This could either be in the form of a bonus should they deliver well in advance of what they estimated or in the form of a penalty if they are delayed. This helps in getting your suppliers to stick to the agreed lead times;
- Automate your inventory management process: Speed up your time to market by automating your inventory management workflows. With tools like QuickBooks Commerce, you can reduce the time taken to create and manage purchase orders, always be in contact with your suppliers, and keep track of stock levels, all without worrying about manual data entry and human error;
- Go local: Shipping products from international suppliers increase lead time. Finding local suppliers could help reduce your lead time significantly.
Reducing lead time is important to help forecast sales, improve customer satisfaction, and improve efficiencies in your operational workflows. QuickBooks Commerce’s inventory management software automates your supply chain, making purchasing effortless and error-free. Manage your lead time and optimize your inventory today.
The Significance of a Short Lead Time: Enhancing Customer Satisfaction and Operational Efficiency
A short lead time holds substantial importance as it profoundly influences various aspects of a company, encompassing financial viability, customer satisfaction, and operational efficiency. The following examples highlight the significance of a shorter lead time:
- Enhanced Customer Satisfaction: Short lead time ensures prompt delivery of goods to customers, satisfying their desire for timely product fulfillment. By minimizing unnecessary waiting periods, customers experience greater satisfaction throughout their purchasing journey;
- Reduced Obsolescence Risk: Goods with extended lead times are susceptible to becoming obsolete before their production is complete. In contrast, shorter lead times mitigate the risk of products losing relevance or demand by the time they reach the market, ensuring a higher rate of successful sales;
- Decreased Labor Costs: Prioritizing internal manufacturing process review enables companies to identify inefficiencies, eliminating unnecessary labor hours. By streamlining operations, companies can significantly reduce labor costs, optimize resource utilization and achieve greater cost-effectiveness;
- Increased Order Volume: A company with a shorter lead time stands out in the market and attracts more orders, particularly when there is a pressing demand for its product. Given similar product offerings, customers are inclined to choose the company capable of delivering goods expeditiously, providing a competitive advantage;
- Efficient Capital Deployment: Short lead times enable more efficient utilization of capital resources. When cash is tied up in raw materials awaiting processing and sale, it remains inaccessible for other strategic purposes. Minimizing lead time allows for the quicker conversion of materials into finished goods, facilitating faster cash flow and enabling companies to deploy capital more effectively for expansion and strategic growth initiatives.
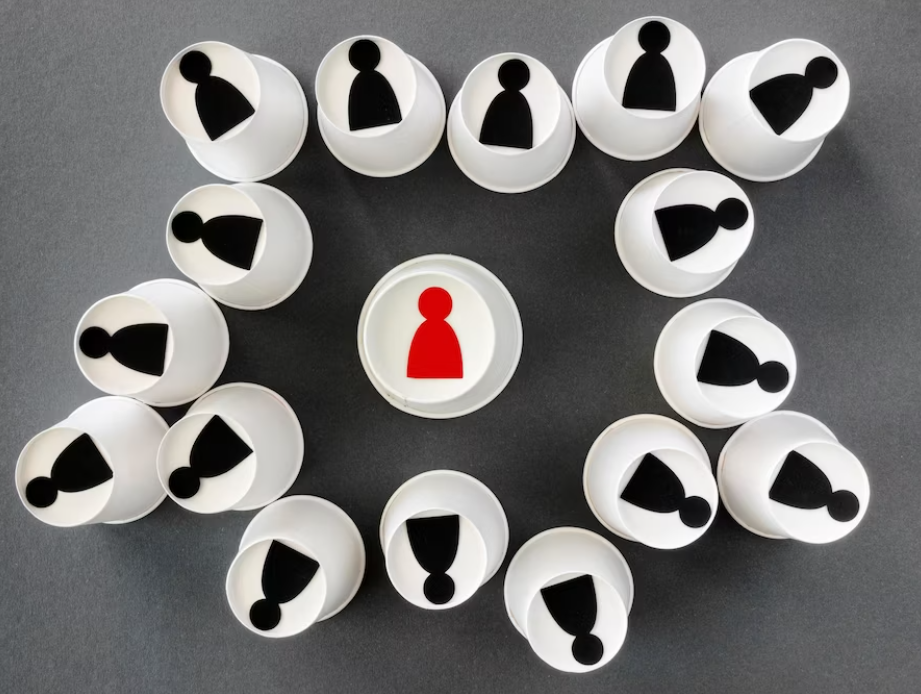
By prioritizing a shorter lead time, companies can enhance customer satisfaction, minimize costs, seize market opportunities, and optimize their financial resources for sustainable growth and success.
Lead Time Type | Description |
---|---|
Customer Lead Time | The time between when a customer places an order and when the customer receives the product. Includes the entire manufacturing process, shipping process, and delivery process. |
Material Lead Time | The time between when a company becomes aware of a need for raw materials and when the materials are physically obtained. May be influenced by information systems, ordering, shipping, delivery, and fulfillment by suppliers. |
Production Lead Time | The time between when a company has all necessary resources on hand to manufacture a product and when it completes the manufacturing process. Depends on internal factors such as waste, labor, equipment efficiency, PPE availability, and machinery downtime. |
Cumulative Lead Time | Aggregated lead time created by combining the above lead times. Used to track different cumulative lead times, such as internal lead time from when raw materials are sourced to when the final product is manufactured. |